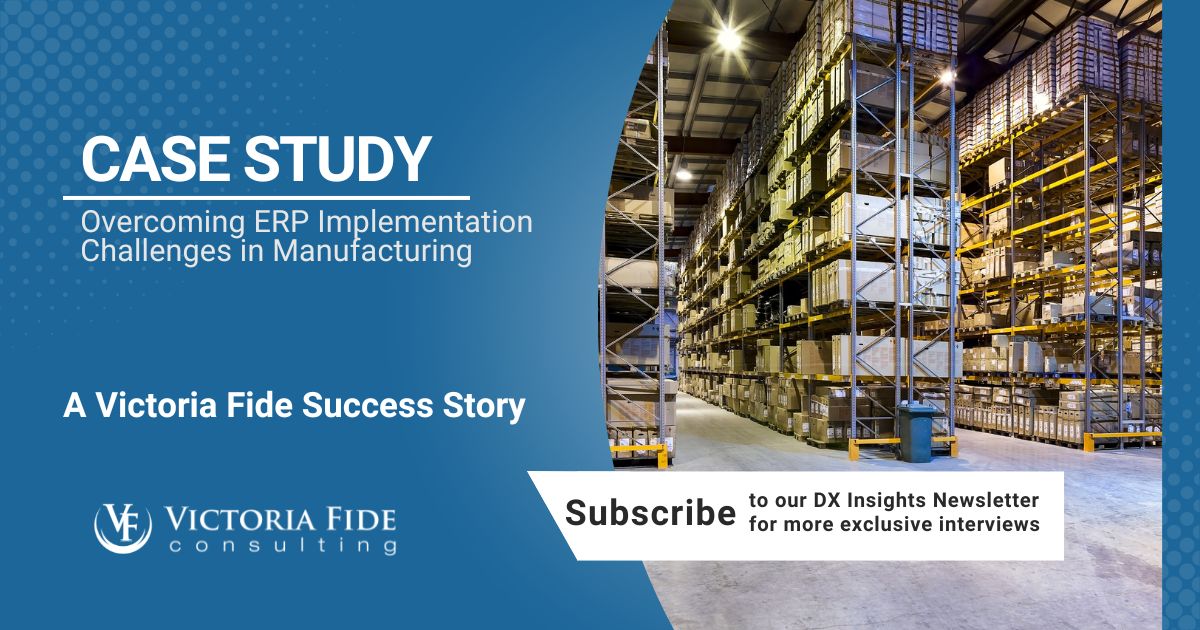
Case Study: Overcoming ERP Implementation Challenges in Manufacturing
In this exclusive interview, Adele Graser, founder and COO of Victoria Fide, takes us behind the scenes of a digital transformation initiative with a previous client: a manufacturing company seeking to optimize their ERP system while wrestling with deeply ingrained mistrust of the system from their team.
Explore how Victoria Fide’s combination of business expertise and digital transformation experience helped encourage long-term user adoption through change management strategies, overcome issues surrounding messy and inaccurate data, and ultimately empower this organization to improve efficiency, provide accurate ship dates for their customers, and optimize their system to support their unique business processes.
Table of Contents
Q: Why is digital transformation so important for optimizing inventory planning, providing accurate ship dates, and efficiently planning production and warehouse work in the manufacturing industry?
In the current supply chain environment where everything is always changing and supply dates are no longer guaranteed, it’s no longer enough to just plan to meet customer deadlines. Instead, companies need to be planning two or three steps ahead. They need to anticipate demand and take steps to meet that demand efficiently or they will find themselves losing business to their competitors.
This is especially true for companies like one of our recent clients who has a global supply chain and utilizes multiple subcontractors for their manufacturing processes. They could no longer rely on receiving items within the same timeframe as they did a few years ago, prompting a need to find a more effective method for anticipating their inventory requirements.
Moreover, after acquiring the inventory, they needed to produce and ship product to their customers faster than before in order to stay ahead of their competitors. This required maximizing efficiency – often with a reduced workforce due to staffing challenges – while ensuring they could meet the promised shipping dates for their customers.
Most manufacturing companies today are facing disruptive supply chains, workforce challenges like low availability and high turnover, and increasingly aggressive customer demands. To address these issues, they must undertake significant digital transformation projects or risk losing to their competition.
Q: Can you describe the process of mapping a previous client’s business workflows to identify areas for optimization? What were the results?
We started by interviewing subject matter experts (SMEs) in each area of their business, from sales and procurement to inventory and production. Using our process catalog with standardized process diagrams, we were able to quickly determine where their processes deviated from industry best practices.
During these interviews, we asked a lot of questions about the issues they faced and, based on our expertise, identified key areas in their processes which were causing those issues. It’s the combination of business acumen and familiarity with standardized best practices that allows our team of experts to cut to the root cause of business issues and develop effective solutions.
Within a few weeks, we developed process diagrams with rich amounts of data that identified problem areas while also highlighting areas that made the business unique. We provided recommendations for “to-be” processes to help them optimize their business operations, better utilize their Enterprise Resource Planning (ERP) system, and preserve their unique advantages – what we call their “secret sauce”.
Part of these recommendations included highlighting data concerns and providing best practices for cleaning up data to ensure their ERP system delivered accurate MRP outputs and reliable customer promise dates. We laid out these recommendations in a roadmap which helped our client make incremental improvements and quickly optimize their largest pain points.
Q: How did the optimizations allow them to provide accurate promise dates, process MRP outputs effectively, and work efficiently in the warehouse? What specific ERP system optimizations or configurations were implemented to generate accurate dates, inventory needs, and potential delays?
We began by optimizing their processes and transitioning them from performing time-intensive manual steps in Excel to more simplified processes within their ERP system. This optimization laid the foundation of accurate information that the system could then leverage for precise forecasting.
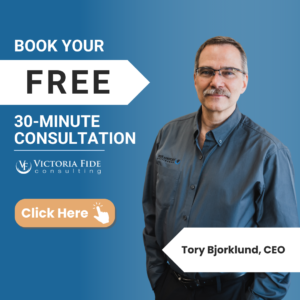
Transformation is not easy, but it doesn’t have to be impossible. Take control of your project’s success today and schedule a free 30-minute consultation to find out how Victoria Fide can equip you for transformational success.
Once the ERP system had accurate supply dates, production routes and times, and customer order data, it was easy to have it begin to provide actionable information. We successfully configured it to provide achievable ship dates for customer orders based on current capacity, available inventory, and incoming supply orders. Additionally, we enabled the system to provide action messages when production was at risk of falling behind due to low inventory or delayed supply orders. This allowed the planning team to focus their time on resolving the exceptions rather than simply keeping standard inventory on-hand.
Q: What specific types of data quality issues were prevalent in their ERP system, and how did these issues undermine trust in the system’s outputs, impacting operations?
This client faced several data quality issues, including missing lead times and planning methods on their items, incomplete or outdated information on their production routes, and a lack of updated dates on their transactions. As we investigated further, we discovered that the data quality issues stemmed from two primary factors: their ERP implementation partner failed to inform the team that certain data fields needed to be populated, and users did not adhere to best practices for updating the system’s data. Due to the incomplete, outdated, or inaccurate information fed into the system, the system in turn generated inaccurate ship dates for their customer orders and improper supply recommendations.
Since they couldn’t trust the MRP outputs or generated ship dates, they began manually planning their supply outside of the system. This required them to either manage their sales information outside the system as well or perform extensive dual entry.
Before long, all core processes and data were being managed manually in Excel, and any transactions conducted within the ERP system required duplicate entry. As a result, the system couldn’t generate any accurate information, resulting in missed production dates, outdated customer order data, and a general lack of visibility into their operations.
Q: Can you provide examples of how the initial ERP implementation was misaligned with their actual business processes?
The initial ERP implementation faced multiple challenges, which led to data quality issues and ultimately the inability to effectively use the system. Firstly, the MRP configuration failed to consider the diverse supply types utilized by the company, including international and domestic suppliers, vendor-managed inventory, and subcontracted manufacturing. Instead, they configured it as a “one-size-fits-all” approach, leading to MRP outputs that rarely matched the specific scenarios that the business encountered.
Secondly, the flexible nature of the manufacturing operations and the need for “on the fly” planning with subcontractors were overlooked. This oversight led to incorrect Bill of Materials (BOM) structures and poorly implemented systems and processes for managing production orders involving subcontracted operations. Lastly, the warehouse configuration was implemented using a standard approach without assessing whether the company needed to track inventory at such a detailed level. This led to complex and inefficient warehouse processes which added no real value to the company.
Q: How did mapping processes help identify optimization needs within the ERP system itself?
By mapping the processes, we identified where users were engaging with the system and where they were going outside of it. Recognizing these deviations highlighted underlying issues within the system that prevented effective use.
This approach allowed us to pinpoint problems with both the process and the system. We then developed a plan to optimize both, ensuring the system could be used effectively while setting the stage for continuous improvements.
Q: What challenges did the company face in terms of getting users to trust and effectively utilize the optimized ERP system?
Effectively utilizing the system presented multiple challenges. The primary issue stemmed from a deep-seated mistrust in the system due to its initial poor impact on their business. Despite our explanations about how the issues were resolved, team members remained more confident in their manual processes, reverting back to them when they wanted to, “make sure it was right.”
Additionally, adherence to standard data maintenance practices was lacking, which led to occasional inaccurate outputs that further eroded what little trust had been built. Finally, training of the new processes also posed significant difficulties. When the processes weren’t followed correctly, errors and inaccurate outputs occurred, eroding the trust even further.
Q: How did you approach change management and user training for the new optimized processes to maintain long-term data quality and process alignment?
Since a general distrust in the system was one of the biggest challenges, we initially focused on explaining how the system worked and showing the reasons behind the incorrect outputs. From there, we brought awareness to business best practices regarding both processes and data management, and ensured they clearly understood why those best practices were critical.
Once both the processes and the system were optimized, we walked the users through detailed testing to help them build confidence in the system. Only after they were completely satisfied with the outputs did they go live with the recommended changes. Afterward, it was important to help them build processes for monitoring their data, validating user compliance with the new process, and addressing any deviations from the process. Additionally, we implemented a process for maintaining the Standard Operating Procedures (SOPs) and training guides to reflect any future changes.
Q: What mechanisms were put in place to maintain data quality and process alignment as business needs evolve?
We developed SOPs on how to create and update items, along with all the supporting information needed for the system to run properly. We guided users in identifying things in the system that indicate incorrect data or non-compliance with processes. Additionally, we ensured they had processes in place for updating their SOPs and training guides whenever changes to their data or processes occurred.
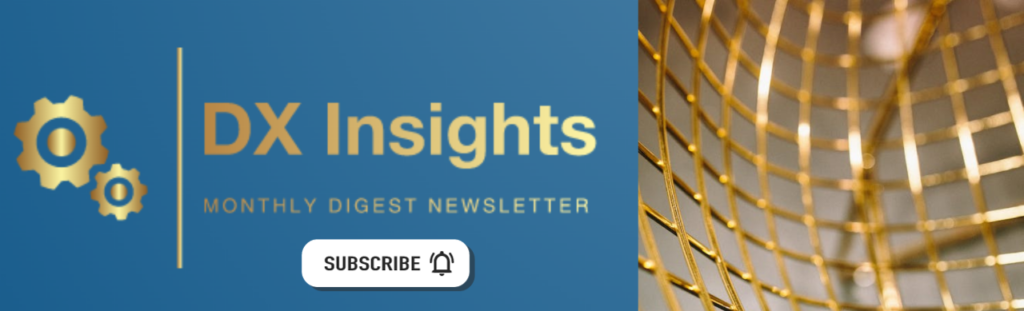
Empowering Your Business for Future Success
This case study highlights several key themes: the importance of aligning ERP implementations with actual business processes, the necessity of building user trust for effective system utilization, and the ongoing need for process optimization and data quality maintenance. These challenges are not uncommon among manufacturing companies seeking to improve their operations through technology, but with the right approach and expertise, they can be successfully overcome.
The client now enjoys a streamlined ERP system that supports their versatile supply chain and manufacturing operations. Enhanced data accuracy has led to improved production scheduling and better inventory management, directly impacting their bottom line, and comprehensive user training and ongoing process monitoring have ensured sustained data integrity and process alignment. In such a competitive business landscape, these advantages provide this organization with an edge over their competitors. Not only do they benefit from the immediate results of more accurate data and efficient processes, but they will also reap rewards for years to come thanks to the careful consideration given to change management and fostering a culture of continuous improvement.
To explore how we can assist your organization with system and process optimization, organizational change management strategies and more, we invite you to schedule a 30-minute meeting with one of our digital transformation experts. Let us help you navigate the complexities of digital transformation and set your business up for success for years to come.